Speakers
Dr Stefan Benkel, Lonza
Dr Andreas Flückiger, F. Hoffmann-La Roche
Rainer Glöckler, Swissfillon
Jorge Guerreiro, Hovione
Dr Rainer Nicolai, F. Hoffmann-La Roche
Dr Andreas Nixdorf, SGS Institut Fresenius
Dr Peter Pöschl, Holopack
Viktor Schnyder, Lugaia
Dr Harald Stahl, GEA
Objectives
The main focus of this conference is on the connection of handling highly potent APIs and the usage of disposable equipment. GMP and safety aspects will be covered and examples from real life will be shown. Amongst others, the following topics will be discussed:
- Definition of the appropriate containment level
- Available single-use components and solutions
- GMP and ATEX requirements for single-use equipment
- Implementation of disposables in pharmaceutical processes
- Qualification of disposable equipment
- Risk handling strategies
Background
The usage of disposable and single-use equipment in the biopharmaceutical production has been growing for years. Well-known examples are disposable bags, hoses and bioreactors. But also in the manufacture of small molecule APIs, the usage of single-use equipment is increasing.
The pharmaceutical industry is now facing a new challenge after a long-time experience had been won with product contact interaction of stainless steel, ceramics or other alloys. Whereas the compatibility of traditional materials is (almost) no topic, plastic material raises discussions. Leachables and Extractables are the big topic here. Many studies have been done already, focusing on effects in aqueous buffer solutions. But coming to the production of small molecule APIs much fiercer conditions have to be considered with respect to organic solvents.
Another issue is caused by the advantages of single-use equipment. It is ready to use and does not have to be cleaned before use. So GMP-relevant steps are shifted towards the supplier of the plastic equipment who has to take care of the GMP-compliant production of his equipment, an appropriate packaging and the necessary documentation. The responsibility remains with the pharmaceutical manufacturer though. Also the handling of disposable equipment is much more demanding compared to robust stainless steel equipment. The training of the production staff gets thus even more important.
Furthermore, the SU equipment does not have to be cleaned after use which is - of course - one of the biggest advantages.
The containment aspect when manufacturing or handling potent APIs is independent from the material of the equipment. The production equipment has to be tight, not only from the GMP aspect to protect the product from the environment, but also from the occupational health point of view to protect the worker from the product. Both have to be proven by measurements.
Yet, with the flexible plastic equipment being much more sensitive to injuries compared to stainless steel equipment, optimised accident scenarios have to be in place.
Besides, there is another advantage of disposable systems. The shift to more single-use systems also brings a higher flexibility to production. More and more single-use isolators are used instead of fixed and immobile isolators - not only to avoid cleaning effort but also to minimize change-over times.
Target Group
Managers and technical experts from production, development and occupational health &
safety, responsible for production, design and installation of equipment, selection and testing of components are the target group of this conference.
Programme
Toxicological fundamentals in the evaluation of highly potent APIs
- Legal requirements regarding worker safety and GMP requirements to control cross
- contamination
- Assessing the hazard: potency and toxicity of APIs and intermediates
- Usage of default values, category- and TTC-based approaches
- Usage of occupational hygiene data in the context of cross contamination control
In this presentation manufacturing steps of small and large scale API manufacturing are
compared and available disposable equipment for each step is shown and discussed
- Processing
- Separation
- Transfer
- Sampling
- Filling
- Film Manufacturing, processing, transportation and packaging
- Clean room conditions for film manufacturing and processing
- Available films and film materials
- ATEX vs GMP certification – how to combine both requirements
- How to seal SU equipment: Crimping vs Welding
- Proof of tightness: SMEPAC measurements
- API and disposable material interactions, biocompatibility
- GMP and ISO certificates
- Designing a L&E study
- Usage of risk analysis tools
- Industrial practice and examples
Using “Single Use Equipment” within the chemical production of API has tremendous advantages, but there are also plenty obstacles to overcome. Typical areas of conflicts are the needs of the production environment such as fulfilling ATEX rules and having a wide range of operational parameters like pressure and temperature versus the unquestionable need of qualifying the material of such systems. As these materials are in many cases different types of plastic there are wide-spread uncertainties how to handle e.g. material certificates.
Case Study Holopack: Implementation of a flexible and single-use Isolator
- Usage of a single-use isolator for open API weighing processes
- Contamination-free transfer
- Safety vs GMP aspects
- Qualification
- Necessary supplier documents (certificates, etc.)
- Containment performance (measurements/results)
- Installations design to manufacture/release potent compounds
- Containment strategies used (practical examples)
- Qualification of the installation / surrogate testing
- Procedures and training
- High Potent classification at Lonza
- Facility Layout
- Safety vs. Quality
- ISO/GMP Classification
- Pressure Cascade
- Single-Use Equipment
- Advantages/Disadvantages
- Equipment used
- Single-Use Experiences
- Operational Hygiene: results
- Single Use in its established environment
- Environment – Health – Safety Policy of Swissfillon
- Implementing “Single Use” into compounding and Final Fill of HPAPIs
- Design Criteria to be met
- Layouts
- Pros and Cons
- Conclusion
This course is part of the GMP Certification Programme "ECA Certified Technical Operations Manager" Learn more
This training/webinar cannot be booked. Send us your inquiry by using the following contact form.
To find alternative dates for this training/webinar or similar events please see the complete list of all events.
For many training courses and webinars, there are also recordings you can order and watch any time. Just take a look at the complete list of all recordings.
Not available
Not available
Not available
Please contact us:
Tel.: +49 6221 8444-0
E-Mail: info@gmp-compliance.org
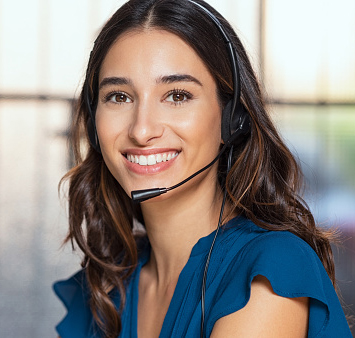
- Our Service
Testimonials
Your Certificate
Seminar Programme as PDF