Speakers
Dr Michael Braun, Boehringer Ingelheim Pharma
Prof Dr Paul WS Heng, University of Singapore
Griet Van Vaerenbergh, GEA Pharma Systems
Objectives
This course aims at explaining were problems in the tableting process come from and how these issues can be avoided or solved. This includes optimisation and trouble-shooting during:
- The development phase
- The scale-up and transfer phase
- The routine and full-scale production
Background
Tableting ranks among the most important pharmaceutical manufacturing processes. Representing about 50% of the total pharmaceutical market, tablets have a particular position. Yet, although tableting is wide spread and used since the invention of the stamp/matrix principle in 1843, there are still open questions and problems in the daily routine which often appear during scale-up or transfer from development. Also in the daily routine with validated processes, issues may arise like for example tablets which suddenly start capping or sticking, or tablets with decreasing hardness or with fluctuations of the content.
Many of these problems originate from the development phase of the tablet and only become visible after transfer to the commercial plant, were usually much bigger and faster presses are used.
The development process should be a holistic approach which takes into account the requirements of a high speed rotary tablet press on its feed materials. The definition of critical process parameters, the selection of excipients based on the mechanical compatibility of API/excipient and the formulation itself must be seen in the full context.
But even after a transfer to the commercial plant, there are some possibilities to get rid off tableting problems, besides lowering the speed of compression. Using coatings, special matrices and stamps or changing the relative humidity or tempering of the tablet press are some amongst others, we are going to talk about. Also the optimisation of upstream processes such as granulation often allows a significant improvement of the subsequent tableting process.
Target Group
This event is designated for all professionals from Pharmaceutical Development and Production, who are responsible for the development, the routine production or the scale-up and transfer of tableting processes.
Programme
Development & Formulation
Mechanical compatibility of excipients and APIs- Basics on the deformation and cohesion in tablets
- Determination of the deformation characteristics using compression analysis
- Explanation of the most relevant excipients
- Classification of excipients in deformation classes
- Finding the right API and excipient combination
- Case studies
In this presentation, the development of an early formulation will be discussed with reference to critical parameters. Such parameters include API load and excipients incorporated together with tablet product characteristics, in particular, hardness and disintegration. Usually, in product development, equipment available in the development department often differs from the equipment used at production-scale. A discussion on the pitfalls of trying to scale-up a laboratory formulation will be presented in this course.
Prerequisites for successful tableting
Essentials for successful tableting
- Mechanism of compaction
- Compaction behavior of pharmaceutical materials
- Granulation
- Mechanisms of agglomeration
- The different granulation types and their influence on the granules’ characteristics
- Influence of liquid and energy input, geometry of equipment etc. on the compressibility
- The compression cycle
- Why formulations from development often make problems
- Modern instrumentation of tablet presses
- The differences of ‘old’ and ‘new’ presses
- Effects of changing the filling time, compression time, circulation speed…
- The influence of tooling
Transfer and Scale-Up
Theory
In this presentation the developed formulation is given to production. Will it work?
Scale-up and transfer from development to production: The Real World
In this session a systematic approach, following QbD principles for scale-up and transfer from development to production will be presented. Case studies focusing on the scale-up of the compression step will illustrate how this can be realized in practice and further look into technical issues and solutions
- Identification and evaluation of Critical Process Parameters and Critical Attributes and link to Drug Product Quality Attributes
- Scale-up principles and transfer strategy
- Case studies
Debugging – make it work
Re-formulation
In this presentation, the initial formulation is re-designed by using the knowledge gained through the presentation. Revealing of parameters which should have been defined earlier:
- Critical quality attributes
- Critical process parameters
- Linkage of CQAs and CPPs for the example formulation
In this interactive session, all the key elements of the preceding lectures are brought together. A systematic approach is presented and discussed with regards to the extent, trouble shooting measures have to be escalated: what can be done on the operator level, what can be done on the supervisor level, what must be done by development:
- Reasons for capping and what to do
- Reasons for sticking and what to do
- Reasons for lamination and what to do
- Reasons for variations in weight and what to do
- Reasons for failing in hardness and what to do
- Reasons for failing in disintegration and what to do
This course is part of the GMP Certification Programme "ECA Certified Pharmaceutical Development Manager" Learn more
This training/webinar cannot be booked. Send us your inquiry by using the following contact form.
To find alternative dates for this training/webinar or similar events please see the complete list of all events.
For many training courses and webinars, there are also recordings you can order and watch any time. Just take a look at the complete list of all recordings.
Not available
Not available
Not available
Please contact us:
Tel.: +49 6221 8444-0
E-Mail: info@gmp-compliance.org
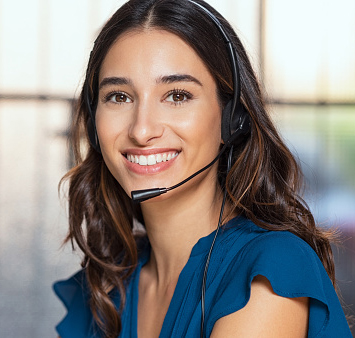
- Our Service
Testimonials
Your Certificate
Seminar Programme as PDF